Hear our client Hog Fuel talks about how the Morbark Industrial Horizontal Grinder, Wood Hog 3400XT, is pivotal to their success.
Article published on Deals on Wheels Issue 342
The Havelock North green waste recycling business moves mountains of unwanted tree materials from farms, orchards, and forests around the district. Their industrial-sized grinder can chew through up to 10 trees at a time. Controlled by remote control, the operation looks slick: a tangle of trunks and branches becomes a mound of golden mulch in minutes. Burning waste is becoming a thing of the past, according to Hog Fuel operations manager Ross Lamborn.
“The product we make is clean and recyclable. Much of it is turned into industrial wood fuel (or biomass) for large industrial boilers/furnaces. Offset by further plantings, it creates less than five percent emissions. We also make mulch, which is double ground and sold to landscapers, as well as compost.”
Morbark Wood Hog 3400XT
With a steady list of clients and more coming on-board, Ross needed a larger processor. He did extensive research to source the best machine he could find. “I researched all the brands and ended up pricing only one machine and that was the Morbark Wood Hog 3400XT—it’s the Rolls Royce of hoggers,” he says. Ross purchased the Wood Hog from exclusive New Zealand importer and distributor of the Morbark brand, Stevens Group, in Auckland in 2019 and hasn’t looked back.
.
Stevens Group has worked with Hog Fuel to ensure the smooth running of the shredder and provide extensive training and back-up service. “When we deliver a machine, we spend three days training the client,” says Stevens Group, Morbark Industrial sales manager, Travis Tschumy. Loading efficiency Sloped infeed sides and an additional infeed length (60.96cm) gives the operator improved visibility and loading efficiency. Ross gives the Wood Hog a 100% rating for their success. “Our growth is directly due to the massive amount of work the Wood Hog can get through. When people see the volume it runs, they are amazed. It takes less than an hour—as fast as the driver can load—to chew through a mountain of branches. To give you some figures: it will do upwards of 80 tones of waste an hour depending on which screens and product we’re running; we hogged 1680 fully mature apple
trees in two hours and 40 minutes.”
Low Running Costs
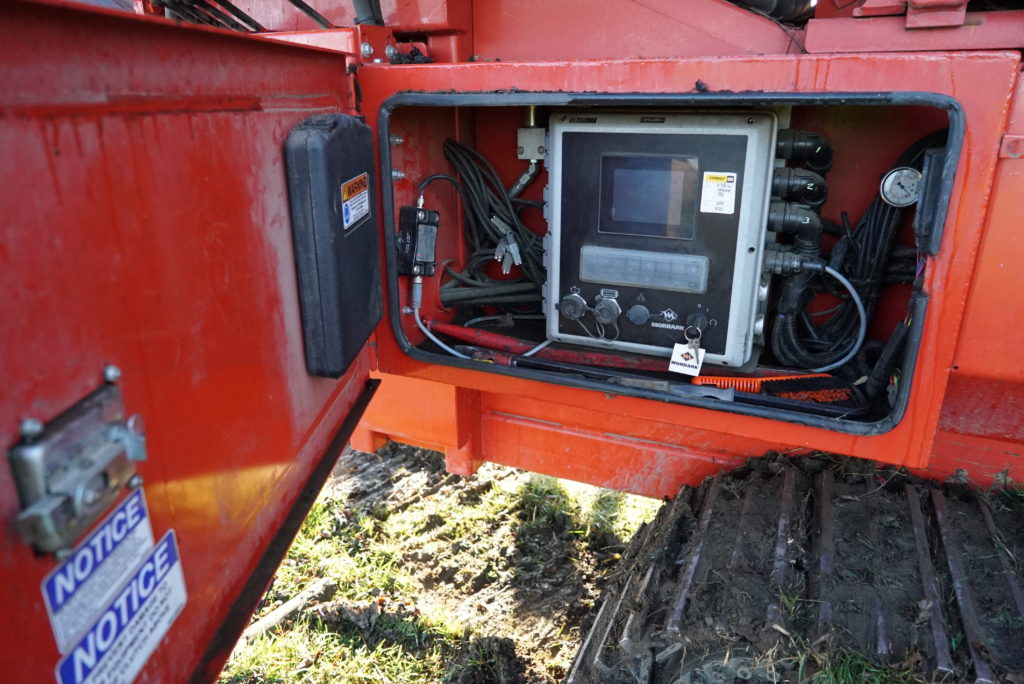
The Morbark Integrated Control Systems (MICS) automatically adjusts feed rates and monitors pressures and feed wheel position to maximise production and engine efficiency.
“There’s a range of other features that set the Wood Hog apart,” says Ross. “It has low running costs. When we first bought the hogger, we budgeted on fuel consumption of 80 to 100 litres per hour, but I don’t think we’ve done more than 50 litres per hour yet. This result is excellent for an 800hp motor, and you’ve got to remember, it’s not like an excavator that doesn’t work all the time; this machine is constantly working. It has amazed us on that count.”
“It’s a straightforward operation to manage, which is good because we don’t have the luxury of downtime. We need to be working all the time. Therefore, it was important to be able to alter anything easily; it takes us 20 to 30 minutes to change the teeth, screens, or grates.” Ross likes that they can produce any end product they want at the touch of a dial. “We can make fine sawdust by changing the grates, the teeth configuration, and the hammers by adjusting a few settings on the computer, or if we need chunky pieces; it’s just as simple.”
Easy to Transport
The Wood Hog is easy to transport and can be narrowed to 2.59 metres, which is within the legal transport width.
“It’s a very clever design; they’ve put a lot of thought into its manoeuvrability and transportation. Because this model is not over-width, you can transport it without a pilot vehicle.”
Maintenance
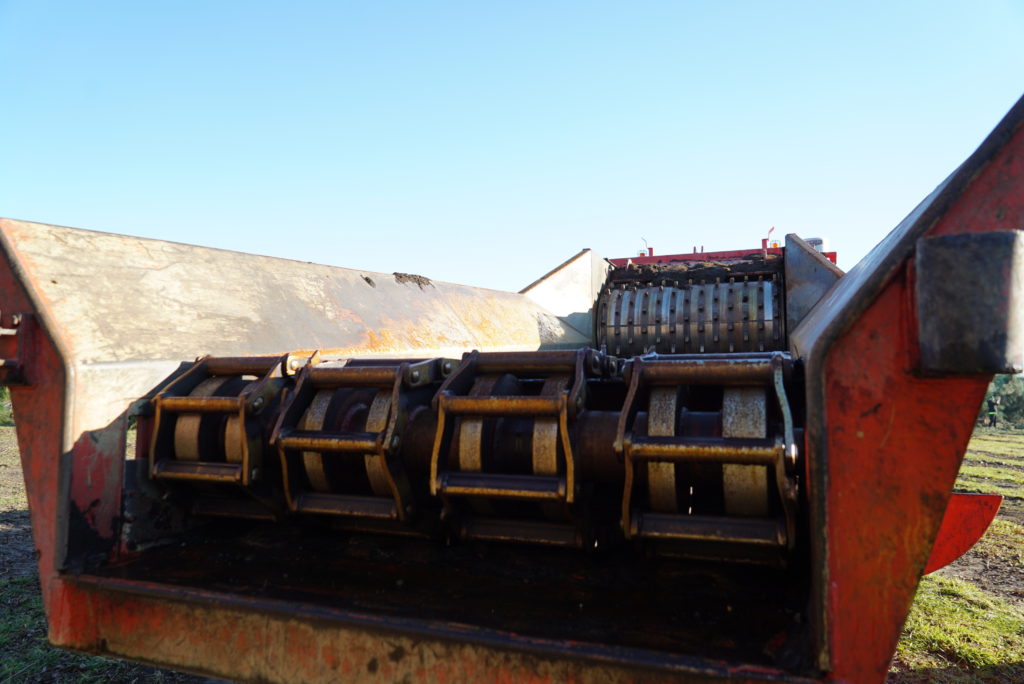
Other features include an extended platform area for maintenance, hydraulic hinged door for changing grates, internal
planetary drive with no chains, or sprockets for lower maintenance.
“The Wood Hog doesn’t have a huge number of moving parts, and this contributes to its low running costs. I’ve had clients getting up to 250 hours of work from an insert before it wears out. Apart from the general servicing such as grease and oil changes for the engine, there are 18 inserts and 18 rakers. For inserts, you’d usually look at new ones every 50 to 100 hours. Rakers can be built back up. You tend to replace hammers and rakers about
2000 hours. The grates, depending on the materials, are replaced at one to 2000 hours.”
Ross adds he’s impressed with the whole operation and can’t fault it. “The Wood Hog just amazes us all the time. When we do something different, I think, maybe this will push it to the limit, but it never does. We absolutely love it. Morbark
have certainly done their homework.”
Family Ties
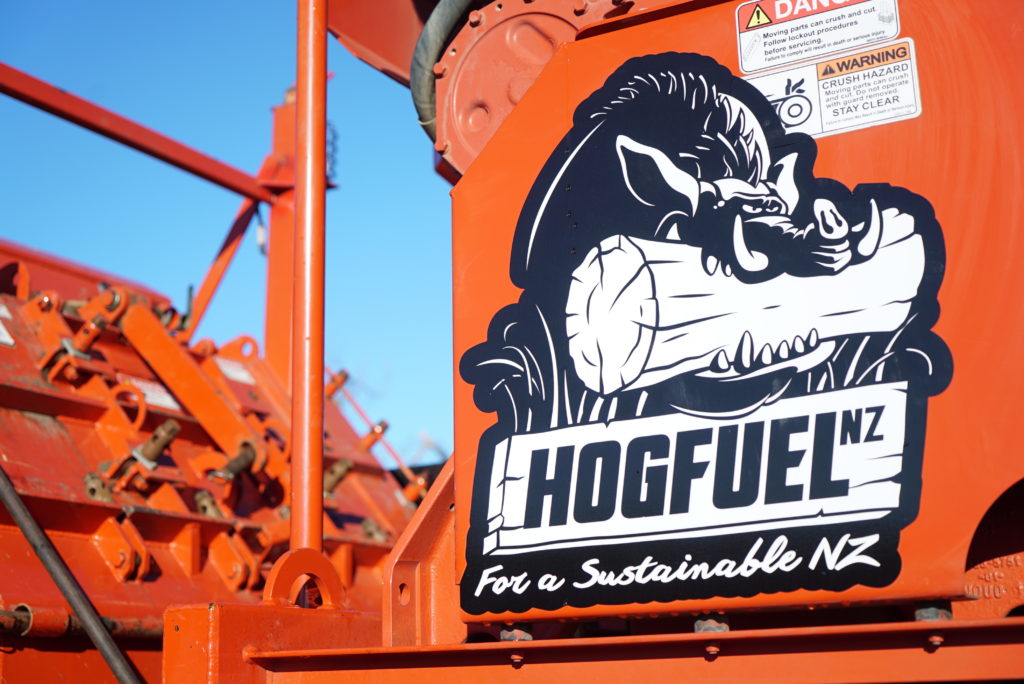
Ross’ father, Jack Lamborn, jumped on-board to support the enterprise as a financial partner. He’s just as excited as Ross about what the Wood Hog can do.
“Dad is an innovator; he gets excited about stuff like this, and he and I feed off each other. I showed him the machine, and because I was so passionate about it, he rang me a week later and said, ‘hey do you want a partner? I can’t stop thinking about it.’ He was so energised. I couldn’t ask for a better partner; he’s the director and I run it. Although he keeps a low profile, he is Boss Hog,” says Ross.
Travis adds, “Hog Fuel has got into the recycling business at the perfect time. Their marketing has been good, and they are a great bunch of guys. I can see them becoming one of the leading companies in the country.”
Stevens Group Ltd.
Stevens Group is a third-generation business and have long been innovators in industrial recycling.
In 2020, Stevens Group added the Doppstadt brand to their impressive reputation as a one-stop-shop for recycling
and demolition machinery. “The new range includes Doppstadt Multipurpose Recycling System, Slow Speed Shredder Line, and Grinder Line. These slowspeed shredders and screening equipment complement the high-speed Morbark shredders in the recycling category,” says Travis.
Of dealing with Stevens Group, Ross says, “We’ve had excellent support from them. Travis has been great; he’s so enthusiastic and loves the product just as much as we do. By bringing in this big gear, Stevens Group is similarly
committed to recycling and pushing for changes within New Zealand as we are.”